Ein bekanntes Szenario von heute: Alarmstufe Rot! Eines der Dauerthemen in der Instandhaltung. Denn irgendwo hakt es immer. Schrillt der Alarm und kommt der Werker an der Maschine nicht weiter, ruft er den Instandhalter. Der denkt dann in verschiedenen Technologien, wie etwa Pneumatik, Hydraulik, Elektrik oder Software. Das Gesamtverständnis der Anlage spielt eine wesentliche Rolle, es geht jedoch technologisch oft wenig in die Tiefe. Wird es etwas „spezieller“, fordert der Instandhalter die Expertin oder den Experten an, etwa einen Software-Techniker oder eine Elektrikerin.
Wartung statt Störung
Wartung ist das zentrale Thema in der Instandhaltung, denn nur die optimale Wartung der Anlagen hilft, unerwünschte Ausfälle und Störungen zu reduzieren. Kommt es dennoch zu einem unerwarteten Gebrechen an der Maschine, ist der Instandhalter gefragt – wenn es diese Funktion im eigenen Unternehmen überhaupt gibt. Diese grenzt dann den Bereich des Problems ein und fordert gegebenenfalls die entsprechenden Fachbereichstechnikerinnen an.
Im Idealfall kann er den Fehler natürlich selbst beheben. Das erfordert aber entsprechendes Fachwissen und vor allem oft auch Spezialwerkzeuge, Messgeräte und andere Tools, wie zum Beispiel eine entsprechende Software. Ist das eine oder andere nicht vorhanden, wird es schnell eng für den Instandhalter. Mit Industrie 4.0 werden sich seine Möglichkeiten bei der Arbeit ändern.
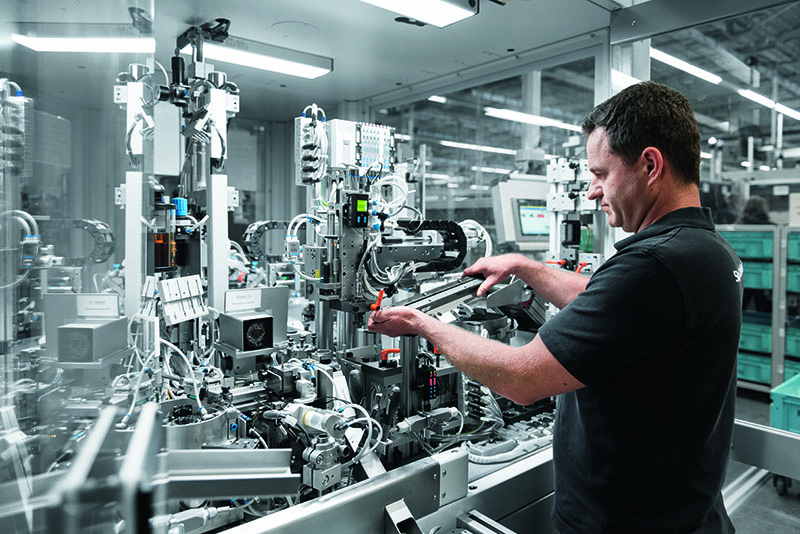
Metadaten, Intelligenz und die richtigen Tools
Maschinen arbeiten künftig hochgradig vernetzt. Intelligente Komponenten und Systeme konfigurieren sich weitgehend selbstorganisiert zur fertigenden Anlage und sorgen so für reibungslose Abläufe. Für den Instandhalter ist – aus der Ferne oder lokal – der Zugriff auf dieses „intelligente“ Netzwerk entscheidend: Er wird immer mehr zum RME, einem Remote Monitoring Expert. Komponenten überwachen sich selbst und speisen unaufhörlich Daten ins Netz. Das ist nicht nur für den Betrieb der Maschine wichtig, sondern auch für die Instandhaltung.
Metadaten sind der Schlüssel zur perfekten Instandhaltung. Ihre Auswertung mit entsprechenden Tools ist entscheidend. Sind Anlagen technisch nicht up-to-date oder wurden die Analyse-Tools nicht von Anfang an mitgedacht, kann die Fülle an Daten schnell zur Herausforderung werden. Immer intelligentere Komponenten integrieren die erforderlichen Routinen daher und bieten dadurch einen Mehrwert, der insbesondere in der Instandhaltung greifbar wird.
Der neue Schraubenschlüssel: IT
IT-Kenntnisse sind für den RME das Um und Auf. Er kennt jeden „Winkel“ seines Maschinen-Netzwerks (IoT) und weiß die Informationen für seine Arbeit zu nutzen. Zudem erhält er automatisierte Warnmeldungen und Service-Anforderungen aus dem System. Virtuelle Lösungen unterstützen ihn bei der Arbeit. Augmented Reality verbindet über das Tablet oder das Smartphone die reale Welt mit der virtuellen. Während die integrierte Kamera Teilbereiche der Maschine aufnimmt, werden Zusatzinformationen über das Echtbild gelegt.
Das können zum Beispiel Live-Maschinendaten sein oder Kennwerte, aber auch Datenblätter, Videos, Fotos oder Software-Tools. Das ist unerlässlich für den RME, denn die hochflexiblen Anlagen von morgen werden sich in ihrem Aufbau und ihrer Konfiguration laufend ändern. Schon morgen kann dieselbe Hardware softwareseitig mit anderen Funktionen belegt sein und sich somit ganz anders verhalten.
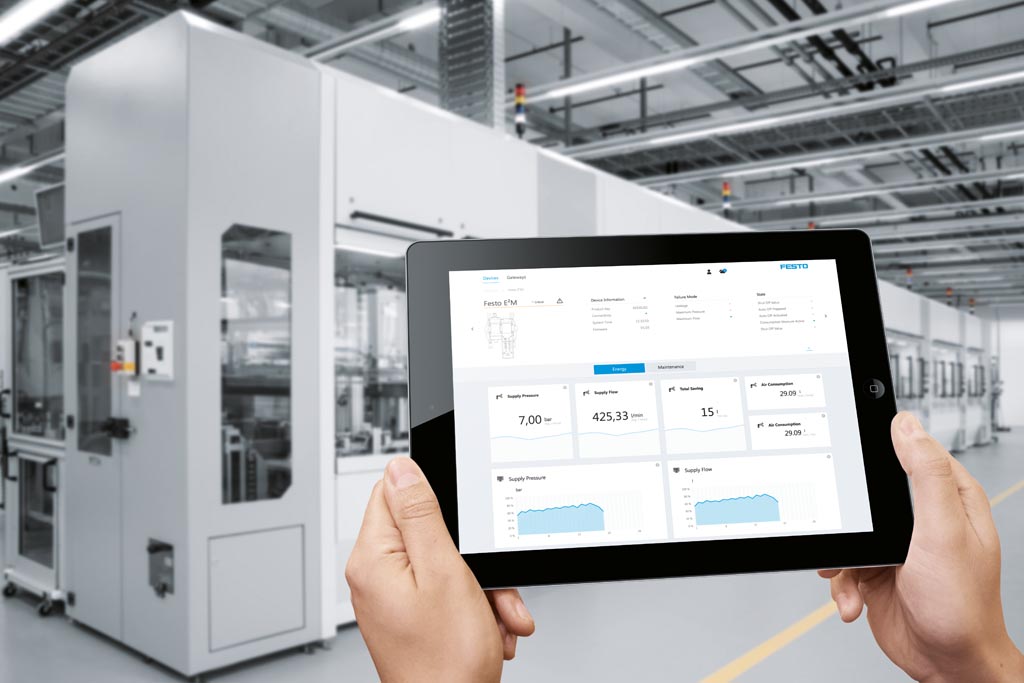
Die Spezialistin vom anderen Ende der Welt
Natürlich können durch die Digitalisierung auch weitere Expertinnen oder Experten hinzugezogen werden, ohne dass diese physisch anwesend sein müssen. Mit einer VR-Brille kann die Spezialistin am anderen Ende der Welt sitzen und bekommt trotzdem in Sekundenschnelle Bilder und Informationen vom RME übermittelt. Dann stellt sie die notwendigen Tools und Anweisungen zusammen und sendet sie an das visuelle Endgerät des RME vor Ort oder direkt an die Maschine.
Die optimale Vernetzung ist also nicht nur für die Maschine von Vorteil, sondern auch für den Remote Monitoring Expert, der sich seine Service-Partner ganz genau aussucht. So geht es Schritt für Schritt von der heute häufig anzutreffenden präventiven Instandhaltung hin zu einer prognostizierbaren – und von der klassischen Instandhaltung zum RME.
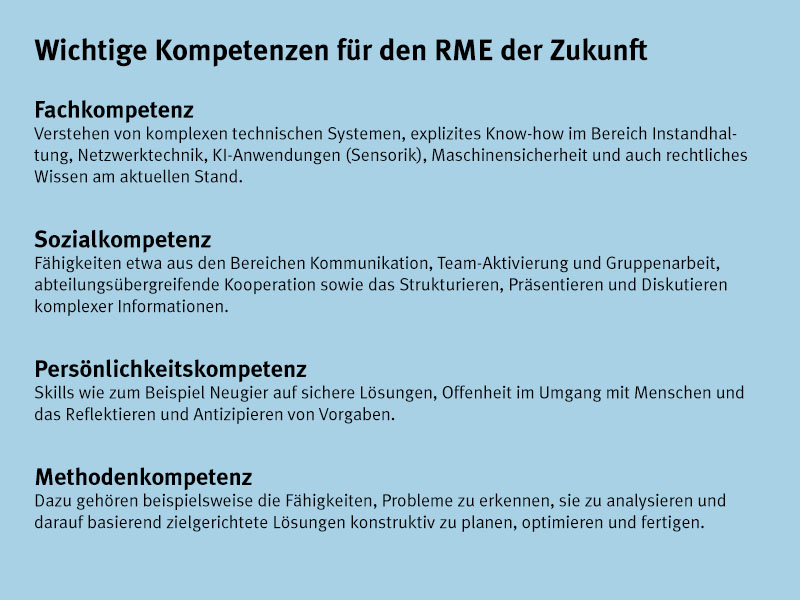
Workshop-Tipp für Remote Monitoring Experts
Cyperphysische Systeme ermöglichen in der Instandhaltung einerseits neue Ansätze, stellen aber andererseits erhöhte Anforderungen. Denn all die Verheißungen von Industrie 4.0 wie One-Piece-Flow oder Make to order sind nur mit einer extrem hohen Verfügbarkeit und Zuverlässigkeit der Anlagen erfüllbar. Bei uns gibt es das passende Know-how – zum Beispiel den Workshop „Smart Maintenance – Predictive und nutzungsabhängige Instandhaltung“. Dort lernen die Teilnehmerinnen und Teilnehmer die Instandhaltungsstrategien der Smart Maintenance kennen. Nach dem Training sind sie in der Lage, Schwachstellen an Maschinen und Anlagen mittels Datenanalyse zu erkennen, das Ausfallrisiko zu bestimmen und im Anschluss geeignete Maßnahmen festzulegen. Dazu können sie die Ansätze der prognostizierbaren und nutzungsabhängigen Instandhaltung nutzen.
Haben wir dein Interesse geweckt? Hier kannst du dich über unsere Seminare informieren und dich direkt anmelden.
TEILEN UND EMPFEHLEN
Hinterlasse einen Kommentar