Für Start-ups ist es oft ein weiter Weg, der meist im Kleinen beginnt. Am Anfang steht eine Idee im Raum, dann folgt eine Vision und dann beginnt die harte Arbeit. So nahmen viele große unternehmerische Erfolgsstorys in einer Garage ihren Lauf – man denke nur an Microsoft oder Apple.
Viel vor, das hatte auch der junge Oberösterreicher Manuel Bernroitner – und zwar von einer Garage in Roßbach aus, die ihm bereits als Kind als Experimentierplatz diente. Schon damals war er fasziniert von Naturwissenschaften und „tollen automatischen Maschinen“. Und so stand sein Berufswunsch schnell fest: Er wollte Erfinder werden.
Mit Erfindergeist in die Zukunft
Gesagt, getan. Außer, dass aus der ursprünglich geplanten, vollautomatischen Wasch-, Trocken- und Bügelanlage, die der Maschinenbauer seiner Mutter versprochen hatte, rund zwei Jahrzehnte später die weltweit erste Anlage zur flüssigkeitslosen Positionierung von Füllstrichen auf Gläsern wurde – etwas, wovon besonders auch die Gastronomie profitiert.
Damit bestimmt genug im Glas ist, werden nämlich die Füllstriche oft vorsichtshalber etwas höher gesetzt, um produktionsbedingte Schwankungen der Glasstärke auszugleichen. Gerade bei einem hochwertigen oder hochprozentigen Inhalt kann das aber deutlich zu Buche schlagen und schnell ein oder sogar zwei Gläschen mehr bzw. weniger pro Flasche ausmachen.
Kleiner Strich – große Herausforderung
„Die Genauigkeitsanforderungen sind in diesem Bereich sehr hoch. Jedoch sind – vor allem bei großen Gläser-Chargen – die Füllstriche nicht immer exakt an der gleichen Stelle, was am Produktionsprozess liegt“, erklärt Bernroitner. „Bei der Herstellung verbleibt oft ein Luftpolster zwischen der Form und dem flüssigen Glas. Dabei kann es zu Konturabweichungen von mehreren Millimetern kommen – vor allem unten beim Stielansatz.“
Eine neue EU-Richtlinie erlaubt allerdings – je nach Glasvolumen – nur mehr eine Inhaltsabweichung von maximal fünf Prozent. Mit dem Effekt, dass man „bei einer hohen Anzahl vor allem kleiner Gläser, wie etwa für 0,1 oder 1/8 Liter, nur mehr schwer gesetzeskonforme Füllstriche setzen kann", erklärt der Jungunternehmer.
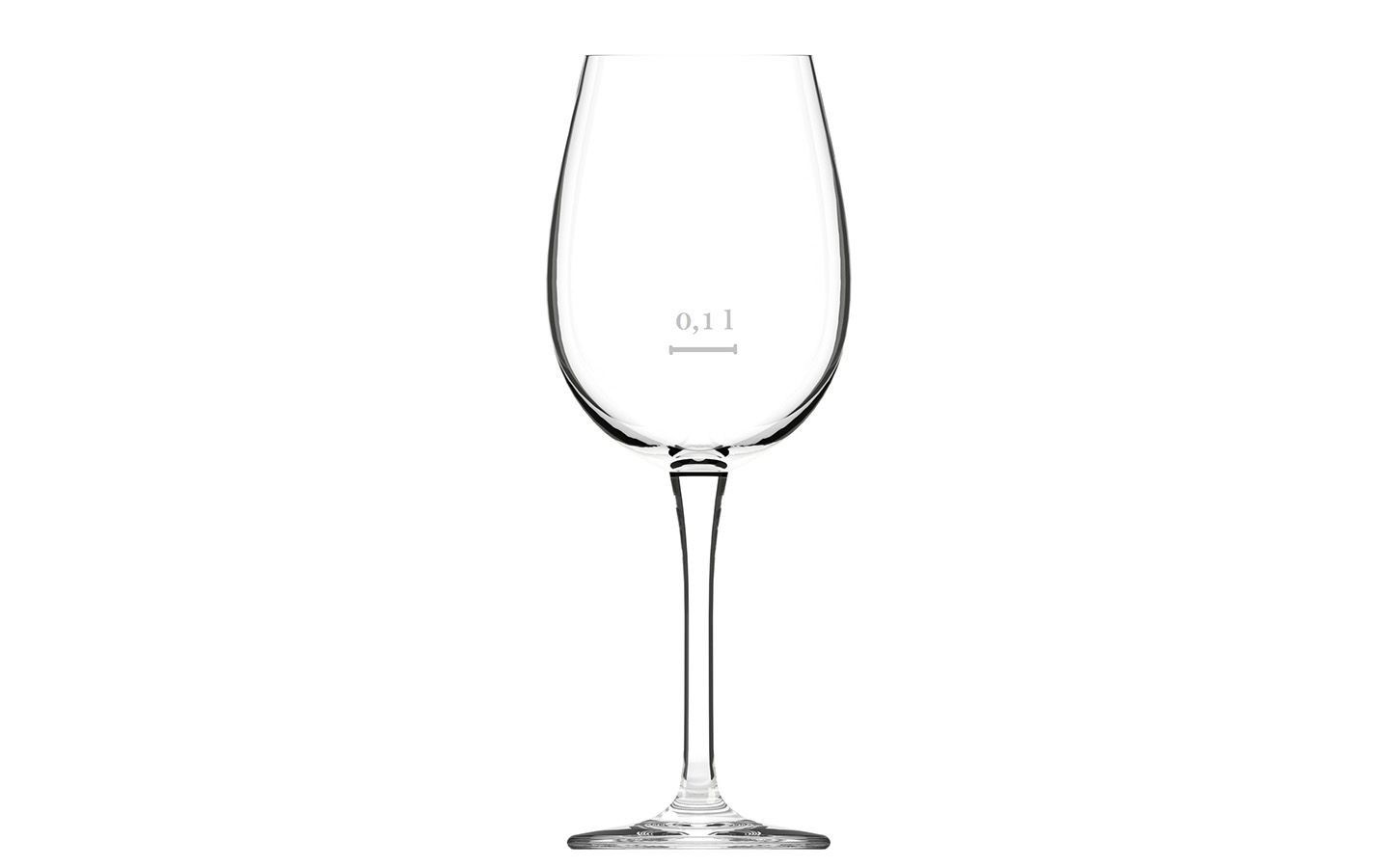
Der Schritt zum weltweiten Patent
Angetrieben von seinem Innovationsgeist überlegte sich Bernroitner schließlich ein neues Verfahren. Das Ergebnis ist die erste vollautomatische Füllstrich-Setzanlage, deren weltweite Patentierung nun eingeleitet ist und in der reichlich einbaufertigen Automatisierungstechnik von Festo steckt.
Nun können Gläser erstmals ohne Flüssigkeitseinsatz und Gefäßverschmutzung vermessen und die Füllstriche punktgenau angebracht werden. „Mein Plan war von Anfang an, bei diesem Prozess auf Wasser verzichten zu können. Denn das Wasser bedingt, dass die Gläser wieder getrocknet werden müssen und das braucht Lagerplatz und kostet Energie. Darum habe ich zunächst eingehend analysiert, welche Möglichkeiten theoretisch funktionieren – von der optischen Vermessung bis zur Ultraschallabtastung“, blickt Bernroitner, heute Geschäftsführer und Gesellschafter der Glass Processing Bernroitner GmbH (GPB), auf seine Tüftlerzeit zurück.
Die Lösung glasklar vor Augen?
Schon bald war klar, welche Lösung die beste ist: „Wir dichten die Gläser ab und saugen die darin befindliche Luft heraus. Dabei messen wir die Luftmenge und schließen auf das Volumen des Glases“, erklärt der 26-Jährige. Vor der Messung wird ein statistischer Zusammenhang zwischen Volumen und Füllstrichposition hergestellt, damit später anhand dieser Berechnungen auf jedem Glas eine möglichst exakte Kennzeichnung erfolgen kann.
Zunächst werden rund 20 Gläser zufällig aus der Charge ausgewählt, ihr Volumen gemessen und die Position des Füllstrichs ermittelt. Diese Informationen werden als Berechnungsgrundlage in die Maschine eingegeben. „Mit dieser neuen Methode erreichen wir beim Setzen der Füllstriche eine ausgezeichnete, zuvor kaum erreichte gesetzeskonforme Genauigkeit und das bei jedem Glas“, freut sich Manuel Bernroitner.
Neuer Prozess mit neuer Präzision
Apropos Genauigkeit. Der Prozess im Detail: Die Gläser werden zuerst manuell oder mittels Roboter in die Maschine eingebracht. Ein Förderband bringt sie zu einer Stoppvorrichtung. Die Gläser werden positioniert, mithilfe eines Handlingmoduls direkt auf die vorhandenen Messköpfe aufgesetzt und dadurch abgedichtet. Dann wird evakuiert – das heißt in diesem Zusammenhang, dass die Luft herausgesaugt und gemessen wird. Dadurch kann die Füllstrichposition des Glases exakt bestimmt werden.
Von den Messköpfen werden die Gläser schließlich auf ein Auslaufband gehoben. Ein Laser bringt im Sekundentakt die Füllstriche „on-the-fly“ an der richtigen Stelle an. Je nach Kundenbedarf kann alternativ auch eine Siebdruckanlage zum Einsatz kommen. Flexibilität wird dabei generell großgeschrieben: So kann die Anlage für Stückzahlen zwischen 400 und 4500 Stück pro Stunde und für ein bis drei Füllstriche ausgelegt werden.
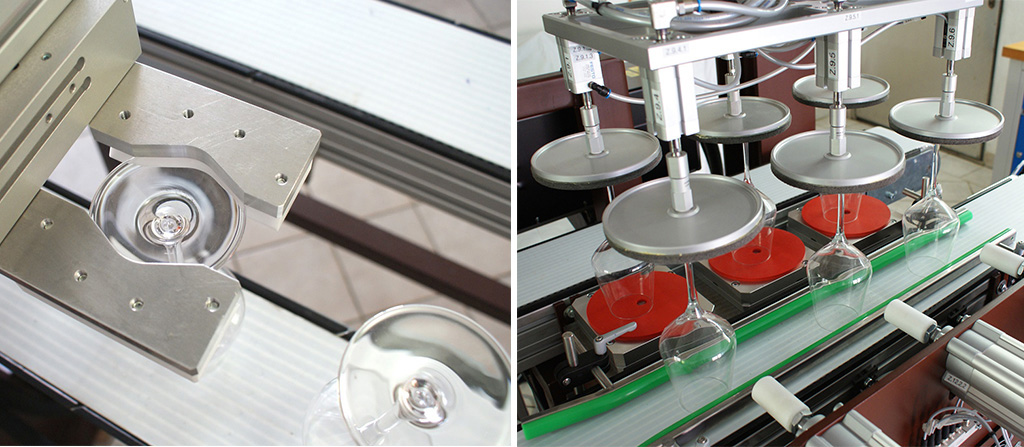
Automation aus einer Hand – effizienter durch Online-Lösung
Für die nötige Flexibilität sorgt unsere elektrische und pneumatische Antriebstechnik. Als Komplettlieferant bringen wir Bewegung ins Spiel. Und diese beginnt bereits auf dem Förderband, das die Gläser – von einem Schrittmotor EMMS-ST angetrieben – sicher transportiert. „Die eingesetzte ServoLite-Technologie macht die exakte Positionierung mit einem geschlossenen Regelkreis möglich. Das heißt, die Gläser müssen danach nicht mehr extra ausgerichtet werden“, unterstreicht Bernroitner.
DSBC-Normzylinder stoppen die Gläser und Vakuumsauger heben sie auf die Messköpfe. Das Vakuum wird durch die hohle Kolbenstange der proportionaldruckgeregelten ADN-Zylinder geführt. Als y/z-Achse kommt beim Aufsetzen der Gläser ein Handling YXCL-3 zum Einsatz.
Konfiguriert hat Herr Bernroitner die Lösung mit dem HGO, unserem praktischen Handling Guide Online. „Das war wirklich hilfreich. Ich konnte eine maßgeschneiderte Lösung zusammenstellen, die Festo dann fertig montiert und geprüft geliefert hat. Darüber hinaus war es möglich, die CAD-Dateien zu meiner Lösung sofort herunterzuladen und in die Gesamtkonstruktion einfügen. Das brachte eine große Zeitersparnis bei der Konstruktion und auch der Montage", sagt Bernroitner.
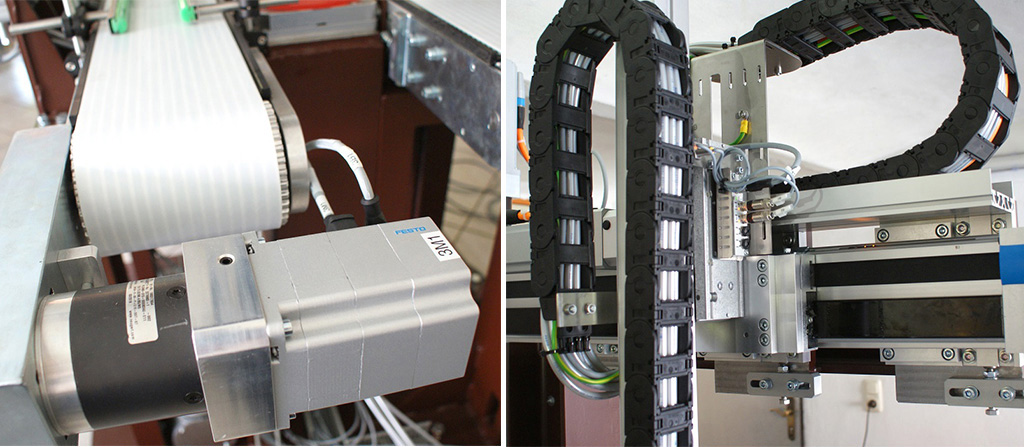
Alles fest im Griff mit IO-Link
Vollautomatisch geht es auch bei der nächsten Station weiter: dem Lasern. Ein HGPL Parallelgreifer hält das Glas dabei genau in Position. Zur groben Höhenverstellung der Laser kommen elektrische Antriebe der OMS-Reihe zum Einsatz. Angesteuert werden alle pneumatischen Antriebe über die Ventilinsel VTUG.
„Mit IO-Link haben wir auf das beste Pferd gesetzt. Die Gesamtkommunikation läuft über ein einziges Kabel, deshalb haben wir uns viel Verdrahtungsaufwand gespart und sind zukunftssicher aufgestellt“, erklärt Bernroitner. Die Druckluftaufbereitung erfolgt mithilfe einer MSB6 Wartungseinheit. Die Ansteuerung der E-Antriebe übernehmen die vielseitigen Motorcontroller CMMO und CMMP.
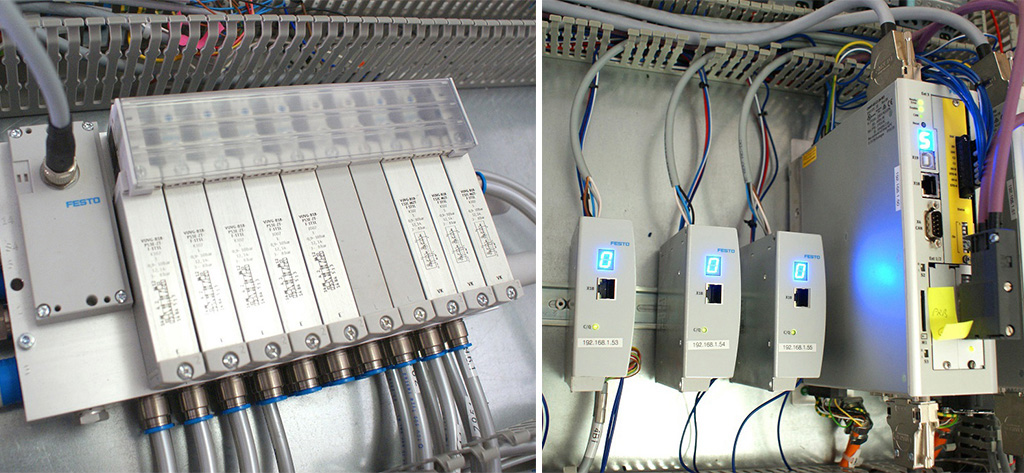
Bestellfertige Lösung
Nicht nur die Komponenten laufen rund – auch die Zusammenarbeit zwischen GPB und Festo funktioniert bestens. „Unsere Erfahrungen waren durchwegs positiv. Ich habe meine Anfrage an Herrn Janata vom Sales-Team geschickt und er hat sie in kürzester Zeit bis ins kleinste Detail ausgearbeitet und sogar weiterentwickelt bzw. optimiert“, sagt Manuel Bernroitner.
Das Ergebnis war eine bestellfertige Automationslösung aus einer Hand, die viele Eventualitäten abdeckt: „Wir können mit unserer Anlage ohne viele Handgriffe die unterschiedlichsten Gefäße verschiedenster Hersteller vermessen und markieren", freut sich Bernroitner über das Ergebnis.
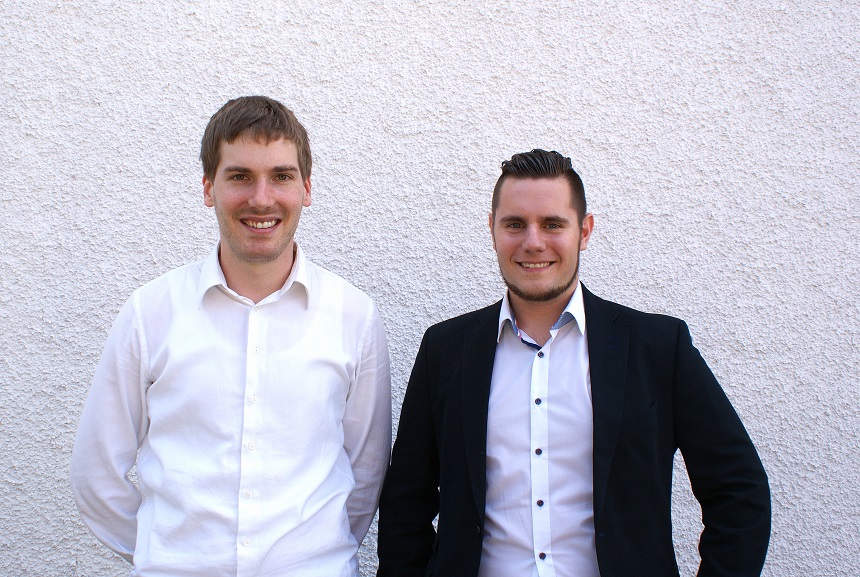
Manuel Bernroitner, Geschäftsführer von GPB und Philipp Janata von Festo Sales
Das Ziel heißt Weltmarkt
Nicht nur die Flexibilität ist ein großes Plus, sondern auch die Ersparnis auf mehreren Ebenen. „Früher musste zum Messen jedes Glas mit einer Flüssigkeit gefüllt werden, um die Füllstrichposition definieren zu können – das war ein riesiger Logistik- und Energieaufwand, der sehr viel kostet und sehr zeitintensiv ist. Dank des neuen vakuumbasierten, flüssigkeitslosen und schmutzfreien Messverfahrens fällt der komplette Nass-/Trocknungsprozess weg“, erklärt Bernroitner.
Und das ist nur der Anfang – der junge Techniker hat Expansion im Auge – der Weltmarkt ist das Ziel. Eine weitere Anlage ist bereits in Planung – der nächste Schritt, um von der Garage in Oberösterreich aus international erfolgreich zu sein.
Für weitere Informationen zum Unternehmen GPB, klicke hier.
Bei Fragen zum Projekt und unseren Anwendungslösungen schicke eine E-Mail an Philipp Janata oder hinterlasse einen Kommentar.
TEILEN UND EMPFEHLEN
Hinterlasse einen Kommentar