Viele größere Flugzeuge erreichen immerhin ein Startgewicht von hundert Tonnen oder sogar ein Vielfaches davon. Daher stehen laufende Kontrollen und eine regelmäßige Erneuerung der Reifen und Felgen auf dem Programm. Die AUA Werft in Schwechat setzt dabei auf die Unterstützung durch Halbrobotik von Roxa Technologies.
Der neueste Coup: Die Modernisierung der vollpneumatischen Manipulatoren mit unserer Servotechnik, und zwar ohne den Einsatz einer zusätzlichen Steuerung.
Interessante Nische als Vorstufe zur klassischen Robotik
Innovatives Querdenken, das ist die Domäne von Roxa Technologies im steirischen Mautern. Eine Halbrobotik-Entwicklung des kreativen Teams sorgt dafür, dass die Wartung von Flugzeugrädern deutlich einfacher wird, damit Passagierflugzeuge sicher abheben und ebenso sicher wieder landen. „Eines unserer Spezialgebiete sind Manipulatoren – das ist ein Begriff aus dem Bereich Hebezeuge und Krantechnik, wo sich alles ums Lasten ‚Manipulieren‘ dreht. Als Vorstufe zum klassischen Roboter hat sich da eine für uns sehr interessante Nische entwickelt, die wir als Halbroboter bezeichnen “, erläutert Horst Gusterhuber, der Geschäftsführer der Roxa Technologies GmbH.
Reifenwechsel alle 300 bis 500 Cycles
Anders als beim Auto, verfügen Flugzeugräder bei allen Flugzeuggrößen über zweiteilige Felgen (Inboard- und Outboard-Half). Die auf diesen Felgen sitzenden Gummireifen müssen auf Grund von Verschleiß rund alle 300 bis 500 Cycles – das sind Starts und Landungen – erneuert werden. Dieser regelmäßige Wartungsprozess erforderte früher von den Monteuren viel Knowhow, Geduld und vor allem Kraft. Daher beauftragte die AUA Werft in Schwechat Roxa 2014 mit der Entwicklung einer Anlage, die den Schraubprozess vereinfacht und auch reproduzierbarer macht. Denn eine genaue Dokumentation jedes einzelnen Arbeitsschritts ist in der Luftfahrt unumgänglich. Automatisierung hilft dabei.
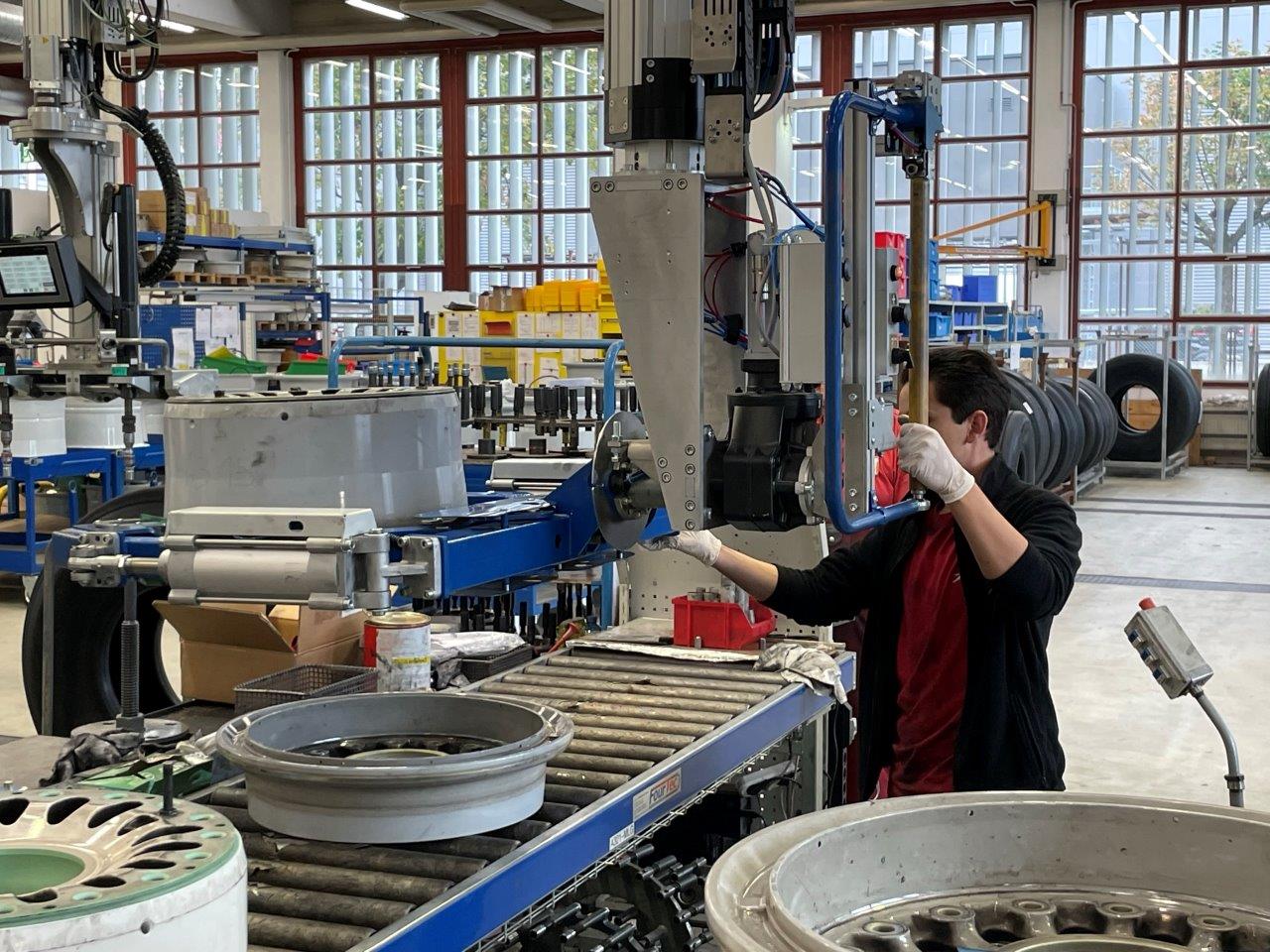
Gemeinsam erfolgreich
Roxa sorgte für das Engineering und der Kärntner Maschinenbauer Kostwein für den Bau der AUA-Speziallösung, die in der gesamten Luftfahrt-Branche auf großes Interesse stieß. Horst Gusterhuber: „Unser Schwerpunkt ist die Entwicklung, Planung und Konstruktion sowie der Vertrieb der Maschinen – den Bau übernimmt unser Partner Kostwein. Da meist auch die Montage und Inbetriebnahme von uns gesteuert werden, gelten wir jedenfalls als Hersteller im Sinne der Maschinenrichtlinie – das bedeutet eine große Verantwortung gegenüber der Airline und ihren Passagieren.“
Felgenhälften + Reifen = Räder
Die Montage der Räder ist eine wahrlich gewichtige Sache. Dabei wird der Unterteil der Felge zunächst mit Hilfe eines vom Werker geführten Manipulators in die Maschine gelegt. Dann wird die Felgenhälfte senkrecht nach vorne gekippt, also aufgestellt. Jetzt werden der Reifen zugeführt und beide Teile zusammen wieder umgelegt, um die obere Hälfte der Felge abzusenken. Am unteren Teil sind bereits die Schrauben mittels Montage-Felgenkranz gesetzt. Die Schrauben stehen mit den Bolzen nach oben und werden „eingefädelt“. Das ist kein „leichtes“ Unterfangen, denn allein die Felgenhälften wiegen jeweils bis zu 130 Kilogramm. Da ist jedenfalls eine ergonomische Unterstützung notwendig.
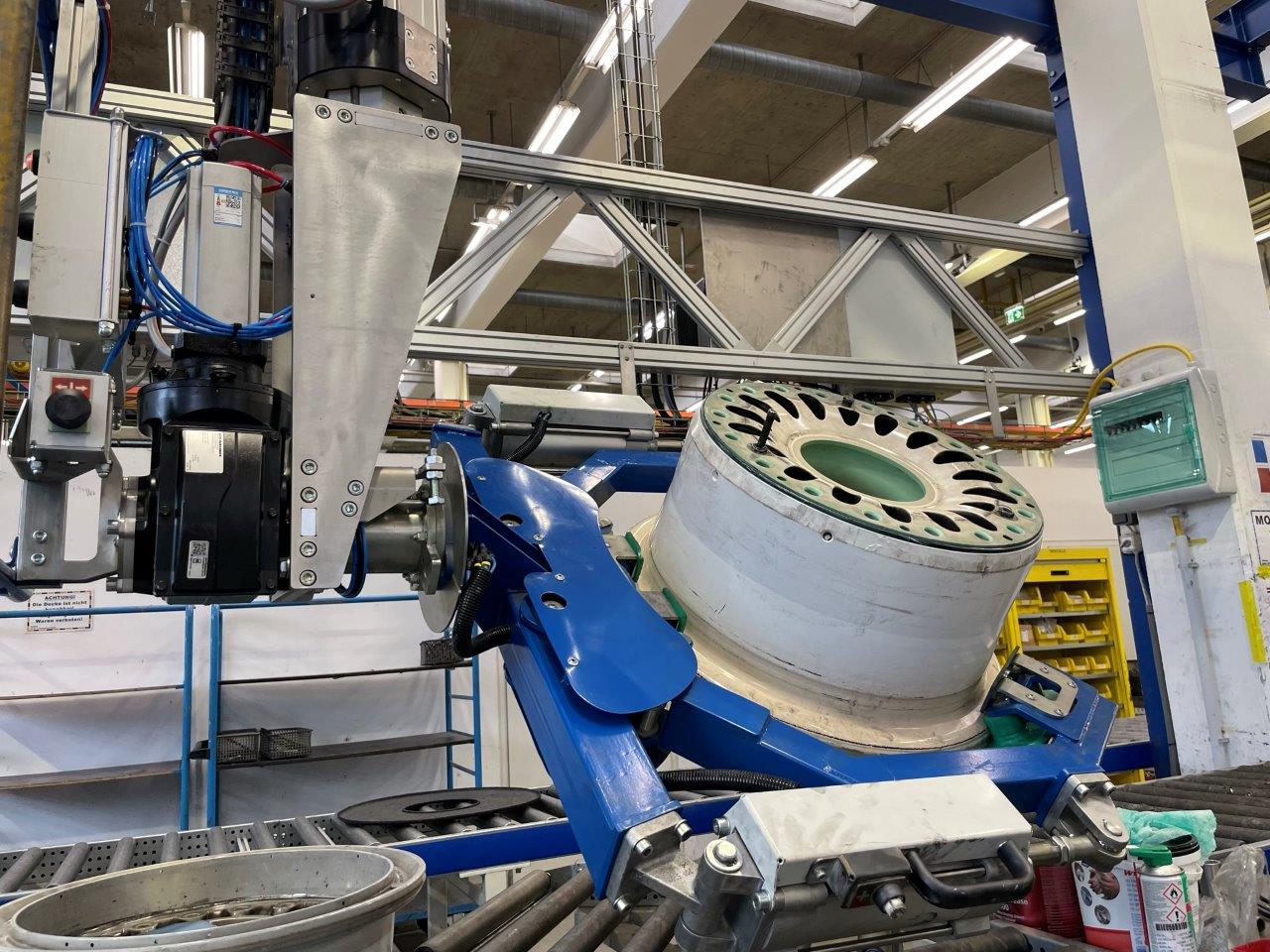
Balance-Akt
Über 40 verschiedene Flugzeugräder müssen perfekt verschraubt werden. Zudem gibt es bei vielen Modellen – wie dem Airbus 320 – auch noch unterschiedliche Konfigurationen und es kommen verschiedene Typen von Felgen mit unterschiedlichen Lochkreis-Durchmessern bzw. unterschiedlichen Schraubenzahlen (8 bis 22) dazu. Diesen Vorgang komplett zu automatisieren wäre extrem kompliziert gewesen. Mensch und Maschine als Team sind daher die beste Lösung. Horst Gusterhuber: „Man kann nicht 120 Kilo halten und dann gefühlvoll 22 Schraubbolzen, die gefedert auf der Unterhälfte stehen, in 22 Löcher einfädeln. Mit Robotern kann man das nicht sinnvoll umsetzen. Da ist – ganz im Sinne unseres Leitgedankens ‚Automatisierung von Menschen für Menschen‘ – der Mensch gefragt. Ihm helfen dabei aber die von uns entwickelten Manipulatoren, die die Felgenhälften sicher in Position zu bringen. Dann beginnt das ‚große‘ Schrauben, das mit von uns entwickelten Lösungen vollautomisch und vollständig dokumentiert von statten geht. Denn es gibt ein genau festgelegtes Verfahren, ein Rezept für jeden Radtyp, das exakt eingehalten werden muss. Dabei ist ein ausgeklügeltes System aus mehreren E-Antrieben und einer schnellsteuernden Proportionalventiltechnik von Festo im Einsatz.“
AUA Werft in Schwechat wartet Räder für die Lufthansa Europa
Dass die von Roxa entwickelte Anlage ein voller Erfolg ist, beweist auch die Tatsache, dass die AUA Werft in Schwechat seit Kurzem der einzige Stützpunkt des Lufthansa Konzerns in Europa ist, wo die Flugzeugräder gewartet werden. Geführt als Profitcenter musste sich die Werft allerdings um diese Aufgabe bewerben und gegen externe, internationale Konkurrenten durchsetzen – was erfolgreich gelang. Aufgrund des dadurch sprunghaft angestiegen Wartungsvolumens und einer erhöhten Anzahl an unterschiedlichen Räder- bzw. Felgentypen – von der kleinen Dash 8 bis zum Airbus 380 – rückte die nächste Ausbaustufe in den Fokus: eine Erweiterung der bisher vollpneumatisch aufgebauten Manipulatoren mit Servotechnik.
Co-Creation punktet
„Wir setzen schon lange auf Festo. Denn wir schätzen die Unterstützung der Experten, wie Gerhard Kogler oder Gerhard Friedl, die selbst bei kniffligen Aufgabenstellungen immer einen Antrieb parat haben.“ Beim Upgrade der Manipulatoren waren auch die Spezialisten des Festo Technic & Application Centers Wien im Einsatz. „Mathias Rapold und Patrick Kahr haben die Lösung vorab im Festo MotionLab als Teststellung aufgebaut und ausgiebig getestet. Die Inbetriebnahme, bei der die beiden Herrn ebenfalls vor Ort waren, ging somit unaufgeregt, in nur zwei Stunden über die Bühne – obwohl diese Umrüstung für uns echtes Neuland war. Eine Zusammenarbeit, die wirklich Spaß gemacht und dank der tollen Umsetzung durch die Festo Techniker rasch zu konkreten Lösungen geführt hat“, unterstreicht Horst Gusterhuber.
Die Aufgabenstellung
Bisher sorgte ein pneumatischer Drehzylinder mit einer vollpneumatisch aufgebauten Maschinensteuerung für das Aufstellen, Drehen und Balancieren der Felgenhälften. Der Manipulator arbeitete also ohne jede Elektrik und ohne elektronische Steuerung – die „Königsklasse“ der Pneumatik. Für kleinere Felgen eine gute Lösung – bei großen, schweren, ständig wechselnden Felgentypen spielt jedoch das Drehmoment eine entscheidende Rolle und das bei einem Lastschwerpunkt der einerseits unterschiedlich und andererseits außermittig ist. Der Verlauf des Drehmoments ist daher während dem Drehen nicht linear sondern sinusförmig. Pneumatisch hätte man das nur bedingt und mit viel Aufwand realisieren können. Zudem war es gewünscht, für Vormontagetätigkeiten oder optische Sichtkontrollen die Felgen während der Drehbewegung sicher stoppen und in jeder Position halten zu können – ein Fall für unsere Servoantriebe.
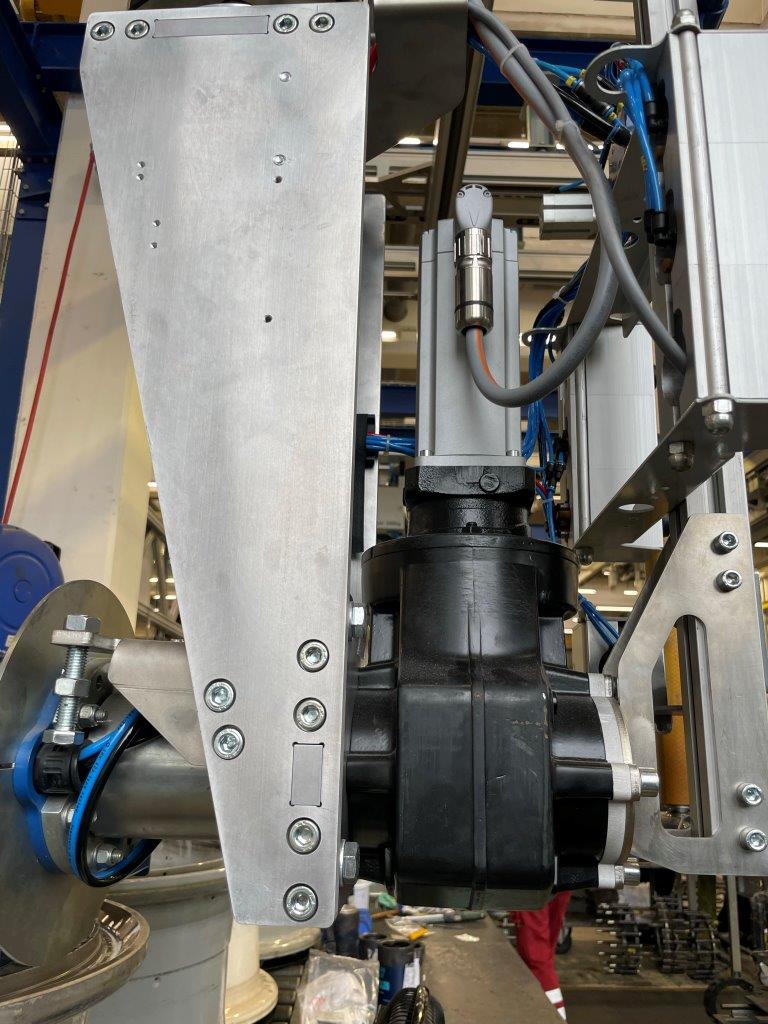
Die Lösung: Servos für die Drehung
Eine Kombinaten des von Roxa entwickelten Hubsystems RX-Lift mit dem Schienensystem RX-Rail sorgt nun – wie auch beim servopneumatischen Schrauber – für die vertikalen und horizontalen Bewegungen. Das Balancieren der schweren Lasten erfolgt dabei grundsätzlich weiterhin pneumatisch mit einer Handkraft, die etwa zwei bis drei Kilogramm entspricht. Dem Bediener wird damit das Gewicht abgenommen und er kann sich voll auf die Bewegungsabläufe konzentrieren. Ergänzt wurde das System bei den Manipulatoren durch Servoantriebe, die nun die Drehung der Felgenhälften übernehmen.
Servotechnik ohne zusätzliche Steuerung
Zum Einsatz kommen unsere Servoregler CMMT-AS und die Motoren EMMT-AS-80 – ein echtes „Dreamteam“, das alle wichtigen Funktionen bereits integriert. Horst Gusterhuber: „Die Kombi – ergänzt mit einem zweistufigen Getriebe – war die perfekte Lösung für diesen bisher rein pneumatischen Anlagenbereich. Die Spannungsversorgung (400V) und Absicherung konnten wir ohne viel Aufwand von den Schaltkästen der Servoantriebe bei den Schraubern übernehmen. Da die CMMT-AS Regler zudem über analoge Eingänge verfügen, war es möglich, die gewünschte Bewegung ohne SPS zu realisieren. Ein großes Plus in Sachen Wirtschaftlichkeit, was dazu führte, dass die Servo-Lösung hier unterm Strich um einiges günstiger war, als eine rein pneumatische Modernisierung.“
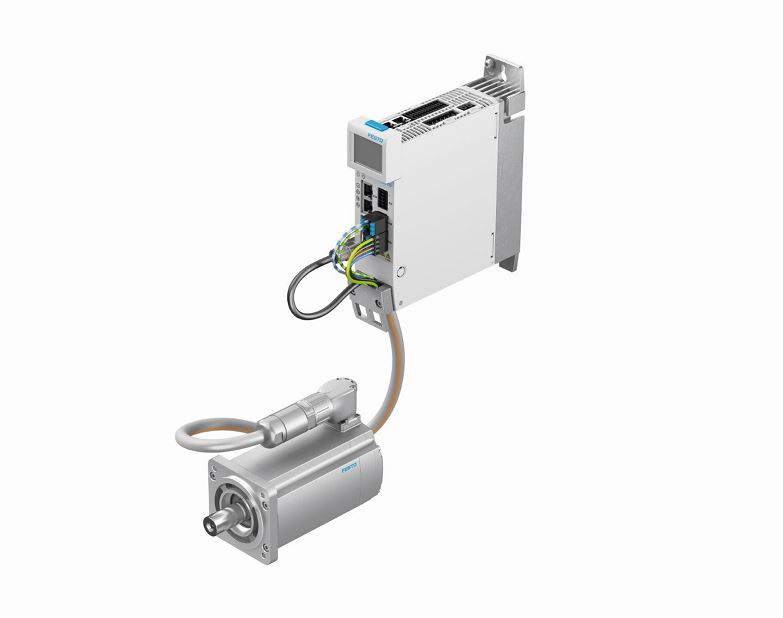
Sicher abgeschaltetes Moment
Die stufenlose Steuerung des Antriebs mit einem Potentiometer in Form eines Daumenrads (mit Richtungssignal) auf einem Joystick ermöglicht es, die Bewegung exakt zu kontrollieren und sicher zu stoppen (STO – sicher abgeschaltetes Moment). Werker können sich daher gefahrlos der „schwebend“ gehaltenen Felge nähern, denn die erforderlichen Standardsicherheitsfunktionen sind beim CMMT-AS bereits an Bord und lassen sich ohne Software konfigurieren. Zweikanalig ausgeführt eine rundum sichere Lösung – auch im Sinne der Maschinenrichtlinie.
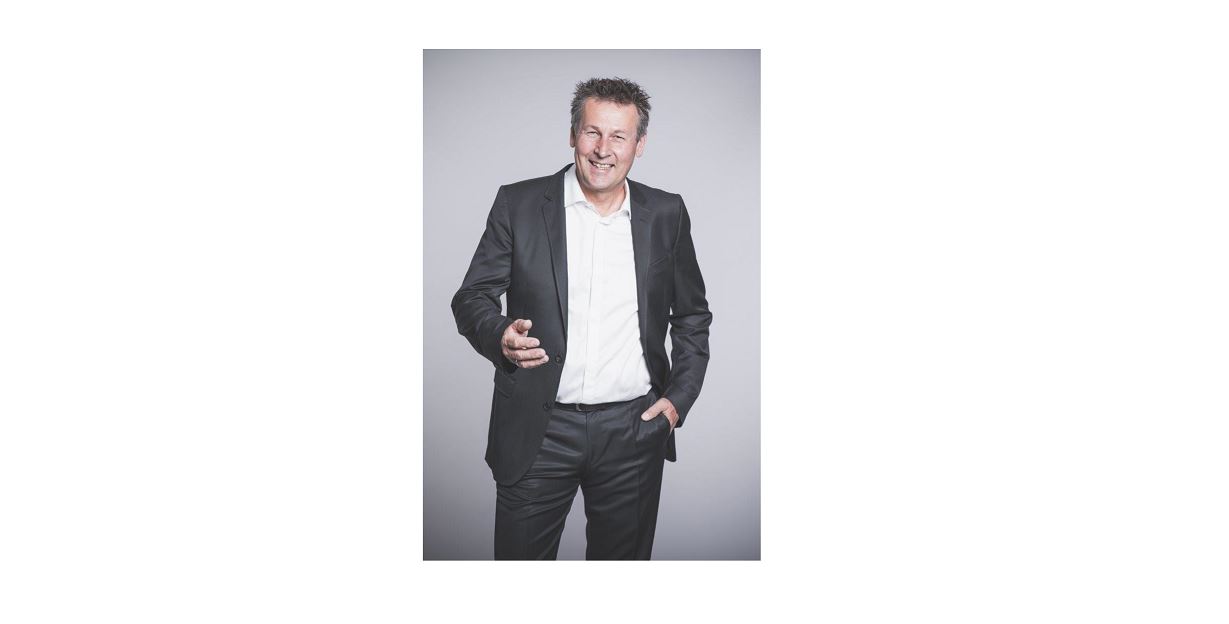
Horst Gusterhuber - Geschäftsführer von Roxa Technologies GmbH
Durchsatz verdoppelt
Die Automatisierung der Zuführung und des Schraubprozesses als durchdachtes Zusammenspiel von Mensch und Maschinen hat sich für die AUA Werft gelohnt. Horst Gusterhuber: „Früher wurden auf den drei Anlagen insgesamt etwa 30 Räder täglich zusammengesetzt – heute sind es doppelt so viele. Bis zu 20 Räder werden nun auf jeder Anlage pro Tag konfiguriert und das mit demselben Personal, das darüber hinaus erheblich körperlich entlastet wurde. Und es können die Räder aller Flugzeugtypen gewartet werden, inklusive einer ausführlichen Dokumentation für alle Abläufe.“
→ Hier findest du mehr Informationen zum Thema elektrische Automatisierung
TEILEN UND EMPFEHLEN
Hinterlasse einen Kommentar