Dabei im Einsatz: Unsere Lernfabrik mit MPS-Stationen, bei denen die Fachkräfte von morgen selbst die E-Planung, die Verdrahtung und die Programmierung der Steuerungen vorgenommen haben.
Flachere Hierarchien, flexiblere Arbeitszeiten, ein höherer Vernetzungsgrad und mehr Eigenverantwortung – so lauten nur ein paar aktuelle Trends der Arbeitswelt, die auch in der Aus- und Weiterbildung Einzug halten. Was das in der Praxis bedeutet, das sieht man bei Hirschmann Automotive in Vorarlberg: Dort ist der klassische Ausbilder zum Coach geworden, der die Jugendlichen bestmöglich begleitet. Vorbei ist die Zeit des Frontalunterrichts. Es geht zunehmend darum, Lösungen selbst zu erarbeiten und aus Fehlern auf dem Weg dorthin zu lernen. Es ist eindeutig zu erkennen: die Lehrlingsausbildung hat sich in den letzten Jahren maßgeblich verändert.
Verantwortung übernehmen
„Selbstständigkeit wird bei uns großgeschrieben. Unsere Lehrlinge müssen sich selbst organisieren, Verantwortung übernehmen und Projektaufgaben gemeinsam umsetzen – das ist für sie ein wichtiger Lernprozess“, sagt Gregor Gspurning, der bei Hirschmann Automotive für die Lehrlingsausbildung im Bereich Elektro- und Maschinenbautechnik verantwortlich ist. „Unsere Lehrlinge werden gefördert und gefordert – wie im echten Berufsleben.“
Fachkräfte selbst ausbilden
Hirschmann Automotive bildet insgesamt über 85 Lehrlinge aus, die verschiedenste Bereiche kennenlernen – von der Elektro- bis zur IT-Technik. „Die Zukunft liegt in der Jugend. Die muss aktiv gefördert werden. Fachkräfte sind bei uns in der Region höchst gefragt, deshalb ist es uns wichtig, unsere eigenen Fachkräfte von morgen top auszubilden“, sagt Gspurning – mit dem Ziel, die Erfolgsgeschichte von Hirschmann Automotive dank erstklassig ausgebildeter Mitarbeiter noch lange fortzusetzen.
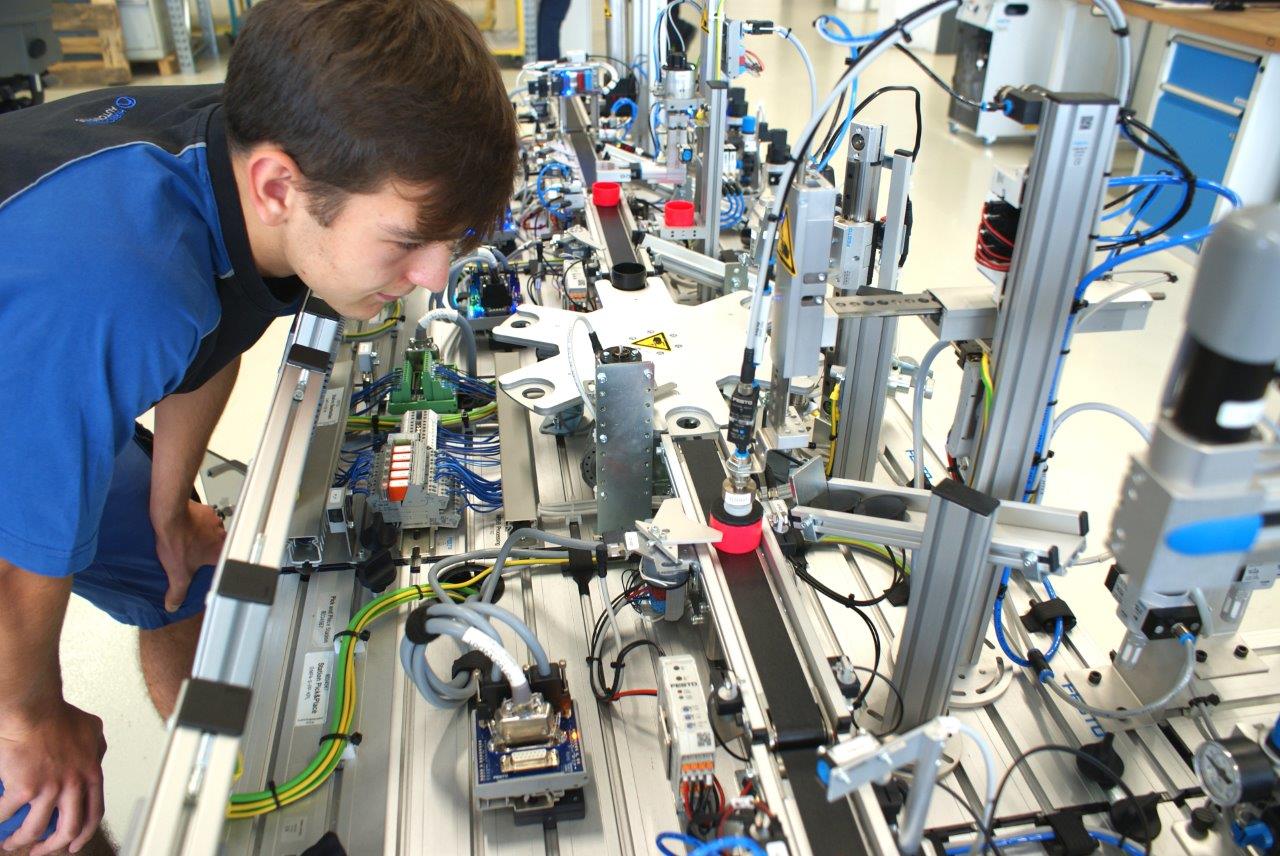
Top Lösungen – top Ausbildung
Die Vorarlberger haben sich in mehr als 60 Jahren mit individuellen Systemlösungen für die Automobilbranche einen Namen gemacht. Das Erfolgsrezept ist ein Mix aus Zuverlässigkeit, Individualität und Innovation. Die Spezialität: Steck-, Kontaktierungs- und Sensorsysteme mit Spezialkabellösungen und modernster Kunststoff-Umspritz-Technologie. Weltweit beschäftigt Hirschmann Automotive mit Hauptsitz in Rankweil rund 5.700 Mitarbeiter an sieben Produktionsstandorten, weshalb die Automotive-Experten auch in der Lehrlingsausbildung ordentlich Gas geben.
Flexibilität durch Modularität
Um ihren Lehrlingen beste Bedingungen zu bieten, die möglichst nahe an der industriellen Realität liegen, setzt Hirschmann Automotive auf unsere Lernhardware – im konkreten Fall auf die MPS-Stationen (Modulares Produktions-System) des Automatisierungsspezialisten. Diese decken alle Bereiche einer modernen Fertigung ab. „Die Modularität der Stationen ist ein großer Vorteil für uns, da wir in der Ausbildung unserer Lehrlinge besonders flexibel sind. Wir können die Kompetenzen und Fertigkeiten vermitteln, die gerade gebraucht werden – technologieübergreifend und in unterschiedlichen Abstufungen. Unser Wunsch war, dass wir die Stationen vom ersten bis zum vierten Lehrjahr zu unterschiedlichen Themen und Aufgabenstellungen verwenden können und das funktioniert mit dieser Lösung ausgezeichnet“, freut sich Lehrlingstrainer Gspurning.
Selbst ist der Lehrling
Die Anschaffung der Lernfabrik war Teil der Ausbildung. Einfach nur kaufen und aufbauen lassen war den Experten von Hirschmann Automotive zu wenig. Die Zusammenstellung und der Aufbau der Lernfabrik waren bereits die ersten kniffligen Herausforderungen für den Technik-Nachwuchs. Sprich: Es galt zu überlegen, was überhaupt angeschafft werden soll und wie aus den erworbenen Mechaniken und Hardware-Teilen ein großes Ganzes – also eine tatsächlich funktionierende Produktion – gebaut wird. Von null auf hundert – in nur kurzer Zeit. Selbst ist der Lehrling! Das wurde hier trainiert und unter Beweis gestellt. Dafür mussten sich Teams finden und auch selbst organisieren – das sind äußerst wertvolle Erfahrungen.
Produktion nach realem Vorbild
Gregor Gspurning: „Die Lehrlinge haben auch die HMIs und Steuerungen entsprechend unserer Fertigung zusammengestellt, sie bestellt, aufgebaut, verdrahtet und programmiert – alles so nahe wie möglich an der Realität. In wenigen Monaten haben sie sich das notwendige Wissen angeeignet und weiterentwickelt“, blickt der „Lehrmeister“ stolz zurück. Wie im echten Leben kam auch hier das Thema Safety nicht zu kurz. Daher mussten sich die Lehrlinge im Zuge der Planung intensiv mit der Maschinensicherheit beschäftigen – genauso wie mit der Wartung danach. Sogar ein Frühwarnsystem mit Wartungszählern wurde eingebaut.
Pneumatik zum Angreifen
Eine kurze Übersicht über den Prozess auf der Anlage: In der ersten Station befördert ein pneumatischer Zylinder kleine Kunststoffbecher aus einem Stangenmagazin auf ein Transportband. Dort wird ermittelt, welche Farbe und welches Material vorhanden sind – gefolgt von der Entscheidung, ob die Teile weiterverarbeitet oder zwischengepuffert werden. Nach einem Qualitätscheck in Sachen Abmessungen geht es erstmals ans Eingemachte: Auf einer Bearbeitungsstation wird das Stanzen simuliert und das Bohren. „Deckel drauf“ heißt es danach. Dafür sorgt ein pneumatisches Handling in Form zweier DGSL Mini-Schlitten und eines pneumatischen Saugers.
Ab in die Box
Jetzt fehlt nur noch die Verpackung: Die Werkstücke gelangen zu einer Schleuse, in der sie vollautomatisch verpackt werden. Die IO-Teile werden mittels Servo-Achse elektropneumatisch in Kartons gelegt und gut verpackt zur finalen Entnahmestation befördert. Der Rest – also fehlerhafte Teile – wurde bereits zuvor über ein T-förmiges Förderbandsystem ausgeschleust.
Übergreifende Zusammenarbeit
Gregor Gspurning zieht eine äußerst positive Bilanz: „Es war toll zu sehen, wie die übergreifende Zusammenarbeit unserer Lehrlinge geklappt hat – auch zwischen den einzelnen Fachbereichen und Jahrgängen. Anfangs war zwar eine leichte Überforderung zu spüren, aber dann kam alles schnell ins Laufen. Dabei konnte jeder von jedem sehr viel lernen.“
Stolz auf das eigene „Baby“
Die Anlage wurde durch die konsequente Mitarbeit zu ihrem „Baby“, wie auch Jakob Nachbaur, Lehrling im dritten Jahr, stolz bestätigt: „Ich war vor allem für die Verbesserung der mechanischen Teile zuständig. Am Anfang war es eine ziemliche Herausforderung. Dann haben wir uns alle richtig reingekniet und am Ende hat alles super gepasst. Es war echt cool und ich habe dabei extrem viel gelernt.“
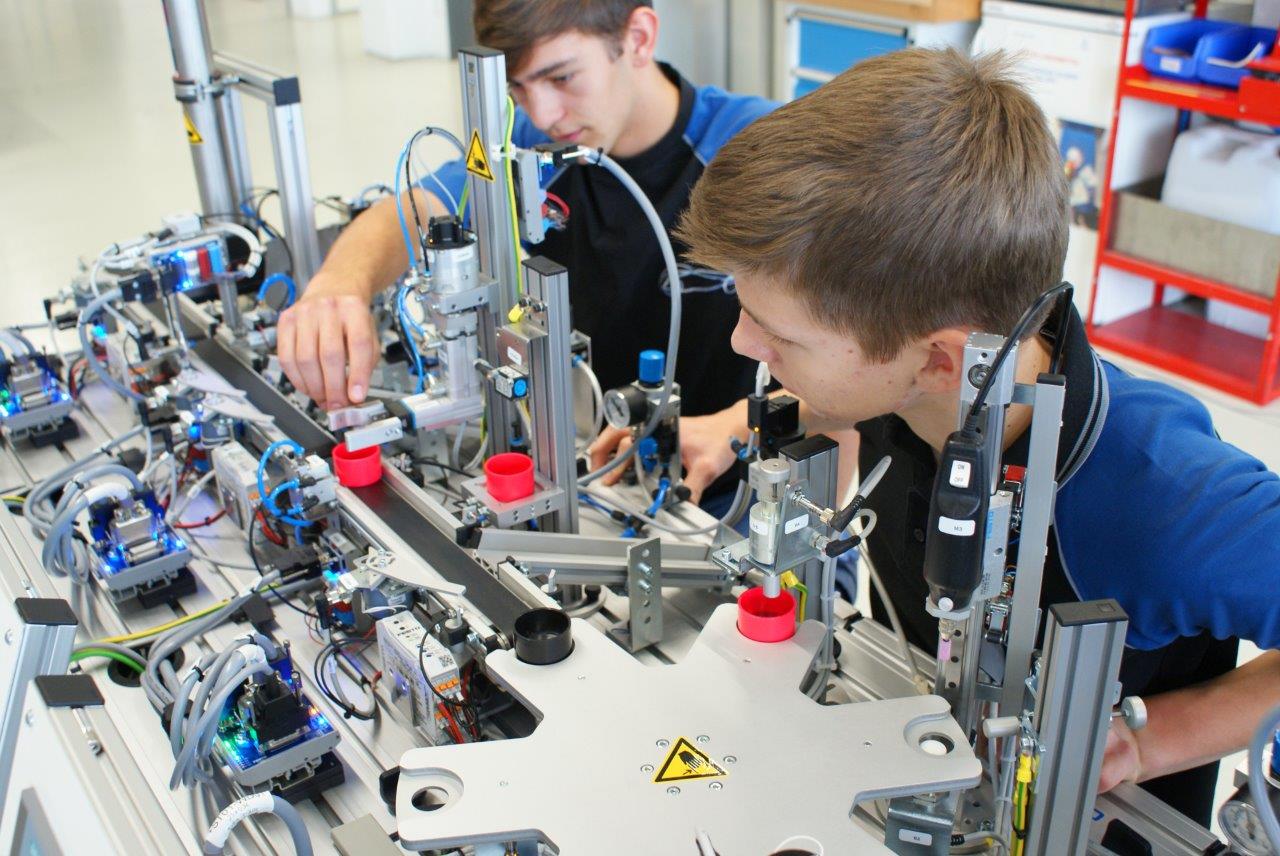
Verdrahtung geschafft!
Begeistert ist auch der Lehrling Tobias Hartmann: „Mein Hauptthema war die Verdrahtung auf Basis der Schaltpläne. das war wirklich anspruchsvoll. Aber wir haben es geschafft und sind jetzt alle stolz darauf. Als nächstes kommt die Vernetzung der Anlage – darauf freue ich mich schon sehr.“
Smarte Transformation
Apropos Vernetzung – seit geraumer Zeit investiert das Vorarlberger Vorzeigeunternehmen stark in die Bereiche Digitalisierung und Automatisierung. Darum soll auch neue Lernfabrik künftig noch smarter werden: „Wir wollen die Anlage weiter ausbauen und die Stationen untereinander vernetzen. Auch hier werden unsere Lehrlinge wieder selbst gefragt sein, selbständig arbeiten und im Team Lösungen finden", so Gspurning. Eine Station soll die Überwachung aller Einheiten übernehmen. Außerdem wird künftig auf RFID-Technologie gesetzt.
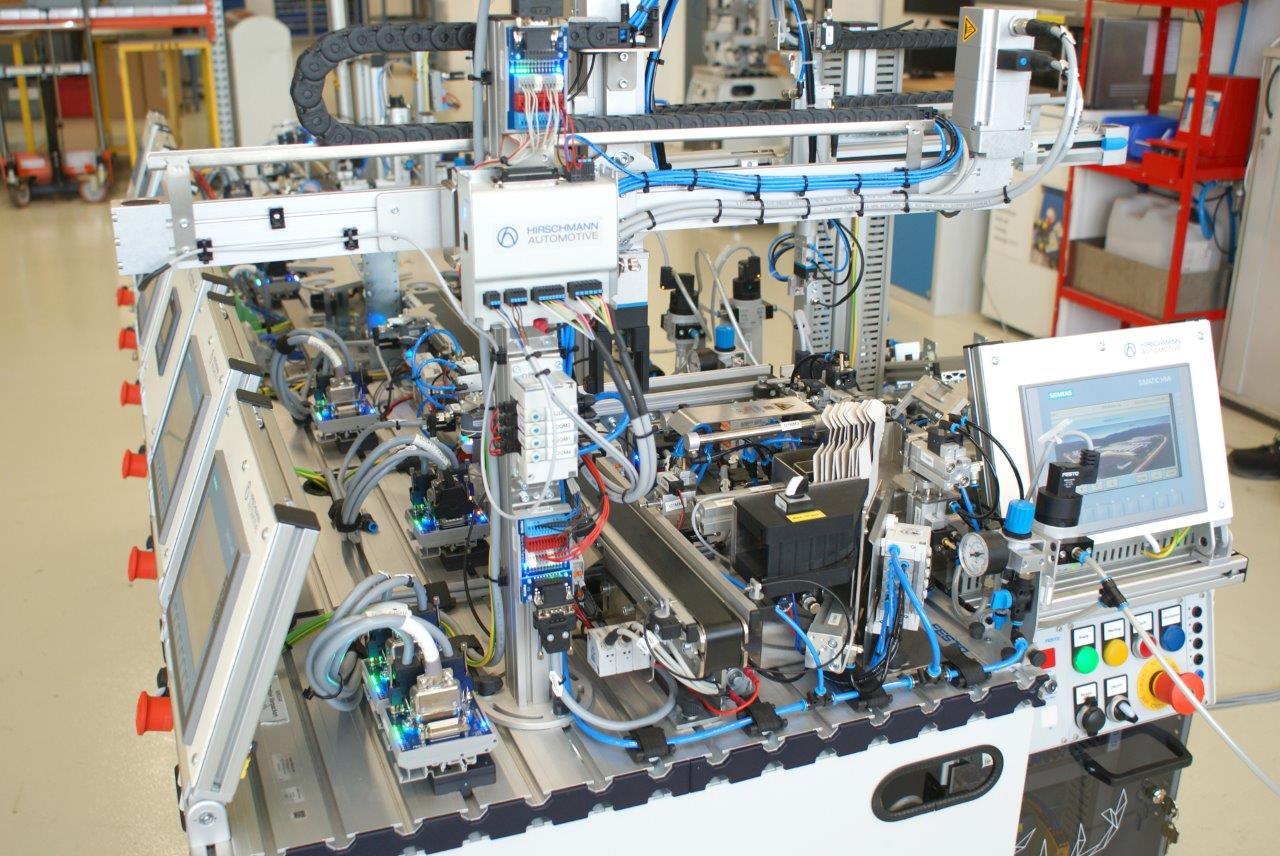
Zukunftsfit
Gregor Gspurning: „Das ganze Projekt ist langfristig angelegt. Unser Ziel ist es, die Lernfabrik Jahr für Jahr zu modernisieren und zukunftsfit zu halten – wie in der echten Fertigung. Die MPS-Stationen sind für uns daher die perfekte Lösung – insbesondere wegen ihrer Modularität und damit verbundenen Flexibilität. Das zeigt sich auch an den offenen Schnittstellen und den Möglichkeiten der Vernetzung. Wer weiß, vielleicht vernetzen wir uns künftig auch mit anderen Lernfabriken, irgendwo auf der Welt. Das wäre ein spannendes Projekt für unsere Lehrlinge und bringt wieder ganz neue Herausforderungen mit sich.“
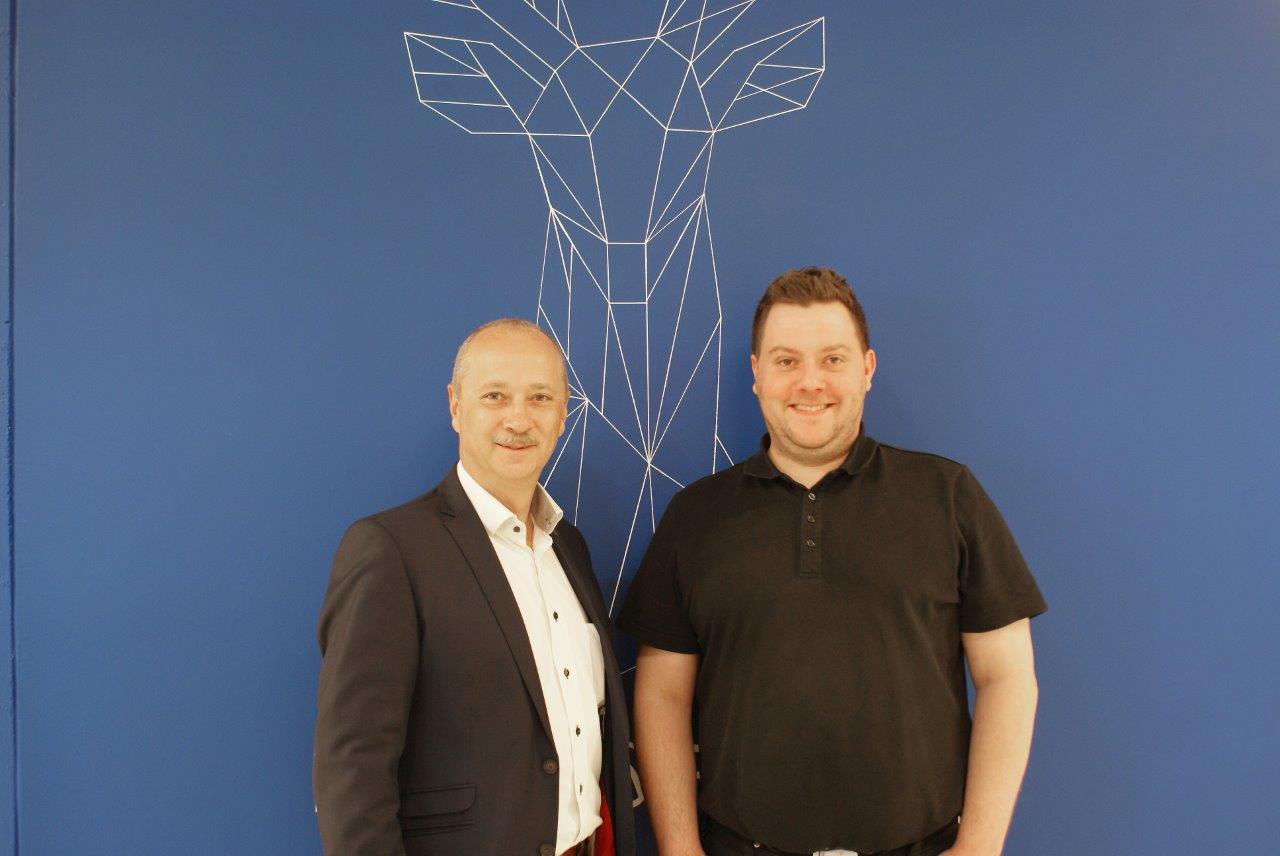
Wolfgang Prähauser (Sales Didactic West bei Festo) und Gregor Gspurning (Ausbilder Elekrtotechnik/Maschinenbautechnik bei Hirschmann Automotive)
Hier findest du einen weiteren Anwenderbericht zur MPS Lernfabrik. Einfach reinklicken!
Du möchstest mehr über unser breites Aus- und Weiterbildungsangebot erfahren? Dann klicke hier!
TEILEN UND EMPFEHLEN
Hinterlasse einen Kommentar